Cotton and polymer go side-by-side in novel fiber
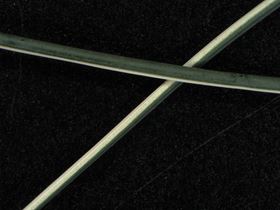
A single strand of fiber developed at Washington State University (WSU) has the flexibility of cotton and the electric conductivity of a polymer called polyaniline.
The newly developed material showed good potential for use as a wearable e-textile. The WSU researchers tested the fibers in a system that powered an LED light and in another that sensed ammonia gas, reporting their findings in a paper in Carbohydrate Polymers.
“We have one fiber in two sections: one section is the conventional cotton, flexible and strong enough for everyday use; and the other side is the conductive material,” said Hang Liu, a WSU textile researcher and corresponding author of the paper. “The cotton can support the conductive material, which can provide the needed function.”
While more development is needed, the idea is to integrate fibers like these into apparel as sensor patches with flexible circuits. These patches could form part of uniforms for firefighters, soldiers or workers who handle chemicals to detect hazardous exposure. Other applications include health monitoring or exercise shirts that can do more than current fitness monitors.
“We have some smart wearables, like smart watches, that can track your movement and human vital signs, but we hope that in the future your everyday clothing can do these functions as well,” said Liu. “Fashion is not just color and style, as a lot of people think about it: fashion is science.”
In this study, the WSU team worked to overcome the challenges of mixing the conductive polymer with cotton cellulose. Polymers are substances with very large molecules that have repeating patterns. In this case, the researchers used polyaniline, also known as PANI, a synthetic polymer with conductive properties, which is already used for applications such as manufacturing printed circuit boards.
While intrinsically conductive, polyaniline is brittle and cannot by itself be made into a fiber for textiles. To solve this, the WSU researchers dissolved cotton cellulose from recycled t-shirts into one solution and the conductive polymer into another separate solution. They then merged the two solutions together side-by-side and extruded the resulting mixture to make a fiber with one side cotton and the other side polyaniline.
This resulted in good interfacial bonding, with the molecules from the two materials staying together through stretching and bending.
Achieving the right mixture at the interface between the cotton cellulose and polyaniline was a delicate balance, Liu said.
“We wanted these two solutions to work so that when the cotton and the conductive polymer contact each other they mix to a certain degree to kind of glue together, but we didn’t want them to mix too much, otherwise the conductivity would be reduced.”
This story is adapted from material from Washington State University, with editorial changes made by Materials Today. The views expressed in this article do not necessarily represent those of Elsevier. Link to original source.
Source link